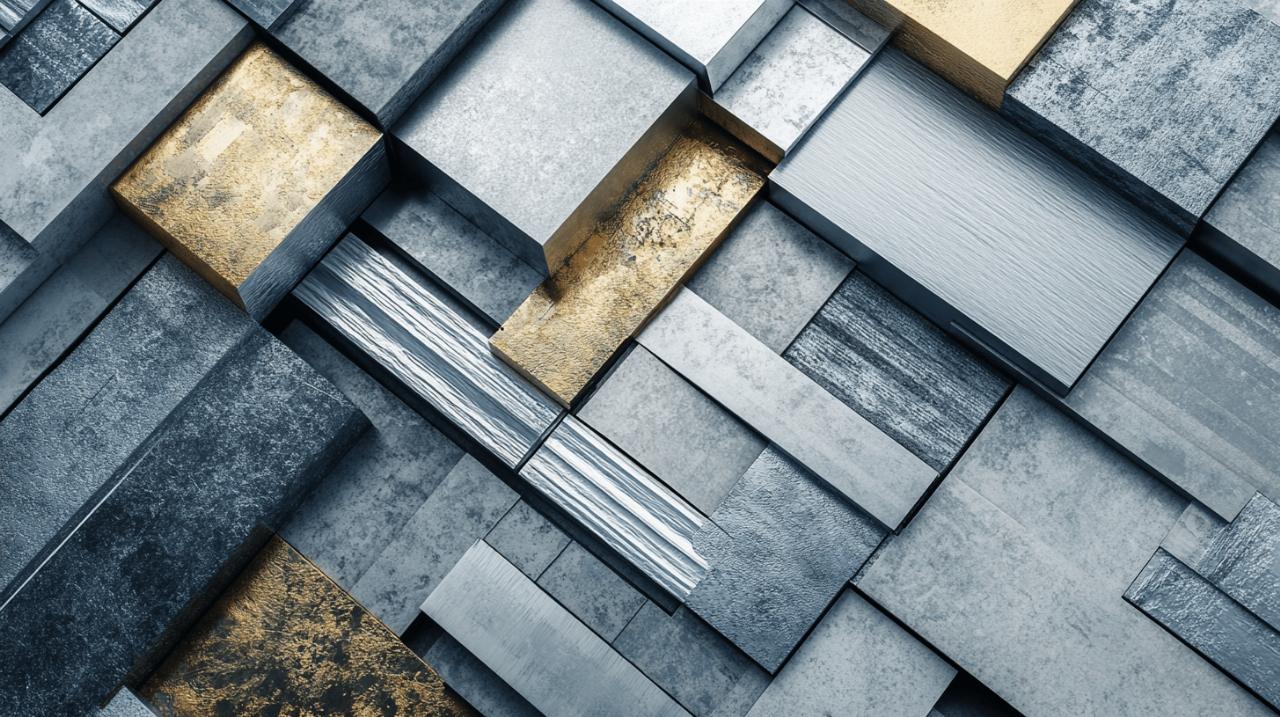
L'industrie de la fonderie d'aluminium repose sur une sélection minutieuse des alliages pour garantir les propriétés mécaniques et physiques recherchées. Le choix d'un alliage adapté détermine la qualité finale des pièces et leur performance dans leur application spécifique.
Les familles d'alliages d'aluminium pour la fonderie
Les alliages d'aluminium se distinguent par leurs compositions uniques et leurs caractéristiques spécifiques, offrant une gamme variée de solutions pour différentes applications industrielles.
Classification des alliages selon leur composition chimique
La nomenclature des alliages d'aluminium s'organise en séries distinctes, chacune présentant des attributs spécifiques. La série 1000, composée d'aluminium pur, offre une excellente résistance à la corrosion. Les séries 2000 à 7000 incorporent différents éléments comme le cuivre, le manganèse ou le zinc, apportant des propriétés mécaniques et une résistance variables.
Caractéristiques des alliages aluminium-silicium
Les alliages aluminium-silicium, notamment les séries A356 et A380, se caractérisent par leur excellente fluidité en fusion. Avec une teneur en silicium variant de 6,5 à 9,5%, ces alliages permettent un remplissage optimal des moules. L'alliage A356 présente une fluidité remarquable, tandis que l'A380 offre une résistance mécanique modérée adaptée à diverses applications.
Propriétés mécaniques et résistance des alliages
Les alliages d'aluminium se distinguent par leurs caractéristiques mécaniques variées, adaptées aux besoins spécifiques de la fonderie. La sélection judicieuse d'un alliage repose sur la compréhension des différentes séries disponibles et leurs applications. Les séries 2000 à 7000 présentent des propriétés uniques, offrant un large éventail de solutions pour la production de pièces moulées.
Influence du cuivre et du magnésium sur les performances
L'ajout de cuivre dans les alliages de la série 2000 garantit une résistance mécanique élevée, bien que la résistance à la corrosion soit modérée. Les alliages de la série 5000, enrichis en magnésium, se caractérisent par leur excellente résistance à la corrosion. La combinaison magnésium-silicium, présente dans la série 6000, comme l'alliage 6061, offre un équilibre optimal entre résistance mécanique et protection contre la corrosion. L'alliage 7075, contenant du zinc, présente la résistance mécanique la plus élevée parmi tous les alliages d'aluminium.
Résistance à la corrosion et traitements de surface
La résistance naturelle à la corrosion varie selon les séries d'alliages. L'aluminium pur de la série 1000 montre une résistance remarquable à la corrosion. Les alliages au manganèse de la série 3000 associent bonne résistance à la corrosion et soudabilité. Pour les applications en fonderie, les alliages A356 et A380, riches en silicium, présentent une fluidité exceptionnelle facilitant le remplissage des moules. La teneur en silicium, comprise entre 6,5 et 9,5%, améliore les caractéristiques de moulage tout en maintenant des propriétés mécaniques satisfaisantes.
Techniques de moulage et paramètres de fusion
Le processus de fonderie de l'aluminium demande une connaissance pointue des alliages et de leurs comportements spécifiques. Les différentes séries d'alliages présentent des caractéristiques variées, adaptées à des applications distinctes. Le choix du bon alliage permet d'obtenir les propriétés mécaniques et physiques recherchées pour la pièce finale.
Températures optimales pour la fonte des alliages
La maîtrise des températures joue un rôle central dans la qualité des pièces en aluminium. Les alliages de la série 4000, riches en silicium, montrent une excellente aptitude à la fusion avec des températures bien adaptées au moulage. L'alliage A356, contenant 6,5 à 7,5% de silicium, offre une bonne fluidité lors de la fonte. La série 2000, associant aluminium et cuivre, nécessite un contrôle précis des températures pour garantir une résistance mécanique élevée.
Méthodes de contrôle de la fluidité du métal
La fluidité du métal représente un facteur déterminant pour la réussite des pièces moulées. Les alliages A380, avec leur teneur en silicium de 7,5 à 9,5%, permettent un remplissage optimal des moules. Les séries 6000 et 7075 demandent une attention particulière au niveau de la fluidité pour assurer une qualité constante. Le contrôle de la composition, notamment avec l'ajout de magnésium ou de manganèse, influence directement la facilité de mise en œuvre du métal en fusion.
Traitements thermiques des alliages d'aluminium
Les alliages d'aluminium présentent des caractéristiques variées selon leur composition. Les séries d'alliages offrent des propriétés spécifiques adaptées aux besoins de la fonderie. La série 7000, enrichie en zinc, assure une résistance mécanique optimale tandis que la série 5000, avec sa teneur en magnésium, garantit une excellente résistance face à la corrosion.
Procédés de durcissement structural
Le durcissement structural implique une séquence précise d'opérations thermiques. La série 6000, combinant magnésium et silicium, répond particulièrement bien à ces traitements. L'alliage 6061 illustre cette capacité avec son excellente résistance mécanique après traitement. Les alliages de la série 2000, enrichis en cuivre, montrent des performances remarquables lors du durcissement structural, offrant une résistance mécanique élevée.
Solutions pour éviter les retassures et porosités
La maîtrise des défauts passe par la sélection appropriée des alliages. L'alliage A356, avec sa teneur en silicium entre 6,5 et 7,5%, présente une fluidité optimale pour le remplissage des moules. La série 4000, riche en silicium, facilite l'écoulement durant la fusion. Le contrôle de la température et la composition équilibrée des alliages comme l'A380 permettent d'obtenir des pièces saines, limitant la formation de défauts internes.
Les applications spécifiques des alliages d'aluminium
Les alliages d'aluminium se distinguent par leurs caractéristiques uniques qui répondent aux besoins variés des industries. Ces matériaux combinent légèreté et résistance, offrant des solutions adaptées à de nombreuses applications. La sélection d'un alliage spécifique s'appuie sur ses propriétés mécaniques, sa résistance à la corrosion et sa fluidité en fusion.
Sélection des alliages selon les secteurs industriels
Les différentes séries d'alliages d'aluminium répondent à des besoins industriels précis. La série 1000, composée d'aluminium pur, présente une excellente résistance à la corrosion. Les alliages de la série 2000, enrichis en cuivre, offrent une résistance mécanique supérieure. La série 3000, avec l'ajout de manganèse, allie bonne résistance à la corrosion et soudabilité optimale. Les alliages 4000, incorporant du silicium, se caractérisent par leur fluidité remarquable en fusion. La série 5000, enrichie en magnésium, excelle dans les environnements corrosifs. Les séries 6000 et 7000 présentent respectivement des propriétés mécaniques équilibrées et une résistance exceptionnelle.
Normes et certifications des alliages de fonderie
Les alliages de fonderie suivent des normes strictes pour garantir leur qualité et leur performance. L'alliage A356, avec sa teneur en silicium entre 6,5 et 7,5%, offre une fluidité remarquable pour le moulage. L'A380 présente une résistance mécanique adaptée aux applications standard. Le 6061, alliant magnésium et silicium, associe résistance mécanique et protection contre la corrosion. Le 7075, enrichi en zinc, atteint les plus hauts niveaux de résistance mécanique. Ces alliages répondent aux exigences spécifiques des industries automobile, aéronautique et maritime.
La maîtrise des défauts dans les alliages d'aluminium
La sélection appropriée des alliages d'aluminium représente un aspect fondamental pour garantir la qualité des pièces en fonderie. Les caractéristiques spécifiques de chaque série d'alliages permettent de répondre aux exigences techniques des différentes applications industrielles. L'analyse approfondie des propriétés mécaniques et physiques guide les professionnels vers les choix les mieux adaptés.
Les techniques d'analyse des défauts de fonderie
Les séries d'alliages d'aluminium offrent des caractéristiques distinctes pour la fonderie. La série 1000, composée d'aluminium pur à 99%, présente une excellente résistance à la corrosion. Les alliages de la série 2000, enrichis en cuivre, se distinguent par leur résistance mécanique élevée. La série 3000, avec l'ajout de manganèse, combine une bonne résistance à la corrosion et une soudabilité optimale. La série 4000, caractérisée par sa teneur en silicium, offre une fluidité remarquable en fusion.
Les facteurs influençant la qualité des pièces moulées
Les performances des pièces moulées dépendent de plusieurs paramètres techniques. L'alliage A356, avec sa composition en silicium de 6,5 à 7,5%, garantit une fluidité optimale pour le remplissage des moules. L'alliage 7075, enrichi en zinc, atteint les plus hautes performances mécaniques. Le 6061, alliant magnésium et silicium, propose un équilibre entre résistance mécanique et protection contre la corrosion. La maîtrise de la température de fusion et la qualité des moules participent directement à l'obtention de pièces conformes aux spécifications techniques.